Otimização de Processos em Six Sigma: Uma abordagem diferenciada de DOE e Taguchi para Green Belts
Nos últimos anos, diante de alta competitividade e recursos escassos, e com o avanço da Indústria 4.0, a estratégia de sobrevivências das empresas está na busca da excelência em Gestão.
Este artigo irá focar em comentar sobre ferramentas poderosas de otimização de processos da fase Improve (Melhorar) em projetos Six Sigma, isto é, após mapeados os processos, tratadas as variáveis que não agregam valor, sistemas de medição resolvidos e capabilidade inicial calculada segundo todo rigor estatístico necessário, é hora de otimizar as variáveis que agregam valor.
Antes de avançar, vamos lembrar a do caminho metodológico que os Green Belts utilizam: DMAIC (Definir, Medir, Analisar, Melhorar e Controlar) até o nível operacional numa organização, seja industrial ou de serviços. São utilizadas ferramentas qualitativas e quantitativas de gestão para tomada de decisão.
Um número expressivo de gerentes ainda não tem consciência das possíveis economias de tempo e dinheiro provenientes de estratégias eficientes de otimização e controle de qualidade.
Uma ferramenta poderosa, o “pulo do gato” que as empresas clamam, e que muitas vezes, infelizmente, sequer são abordadas em muitos Green Belts, e até mesmo superficialmente em alguns Black Belts, é o DOE (Design of Experiments) cujos nomes mais comuns são: Projeto de Experimentos, Planejamento de Experimentos e Delineamento de Experimentos.

Um processo é qualquer sistema onde podemos enxergar variáveis de entrada e variáveis de saída conforme Figura 1. As variáveis de saída são as respostas do processo (Y´s) que precisam ser otimizadas.
Se estivermos falando de lucro, rendimento por exemplo, o objetivo de otimização é de maximização. Mas se estivermos falando de refugo, reprocesso, estoque em processamento, lead time, por exemplo, aí o objetivo é de minimização. Mas se a ideia não é nem maximizar nem minimizar, então o objetivo de otimização seria nominal, é melhor.
Por exemplo, na indústria alimentícia, uma grandeza que sempre nos atormenta é a variabilidade peso de alimentos. Com relação à sobrepeso (que seria um give away), imaginem 1mg sendo produzido 24 horas por dia, 365 dias no ano.
- Qual o custo disso? Sem dúvidas milhares de dólares. Porém, imaginem o contrário, uma determinada variação de peso a menos que o nominal onde órgãos regulamentadores podem autuar com multas devido a clientes lesados.
- Qual o custo tangível e intangível disso? Aliás, dentre várias outras aplicações, seus alunos reduziram variabilidade em peso de alimentos, de forma significativa com impacto de milhares de reais em give-away e reduziram a zero multas por falta de peso em indústrias multinacionais de alimentos de grande porte.
As variáveis de entrada (X´s) são fatores independentes e são manipuláveis com o objetivo de se encontrar o impacto nas variáveis respostas.
Neste ponto é importante destacar que se um processo é qualquer sistema onde podemos entender como variáveis de entrada e saída, peço a seguinte reflexão:
Onde então podemos aplicar esta técnica DOE no dia a dia das nossas empresas?
Sim, a resposta é em tudo, inclusive na área de serviços, onde uma variável que sempre podemos otimizar é o nível de satisfação de clientes ou qualidade percebida pelo cliente.
Exemplificando na área de serviços, uma aplicação que cresce muito nos últimos tempos é a área gestão hospitalar onde o fluxo do paciente é uma das variáveis de muito interesse.
Este pode envolver uma série de gargalos neste tipo de organização, dentre outros: tempo de espera e permanência, custos, demanda e capacidades e taxa de ocupação.
Aqui o cliente final é um paciente que com as devidas proporções comparadas à abordagem industrial onde nasceu o Six Sigma precisa ser liberado com o máximo de qualidade.
Ao contrário da abordagem tradicional, esta abordagem de otimização tem uma série de vantagens
- Requer menos experimentos do que os métodos convencionais de experimentação (uma variável por vez);
- Possibilita a otimização e a modelagem matemática do processo;
- As variáveis são manipuladas de forma matricial e multivariada.
Mas, qual é abordagem tradicional de “otimização” de processos, mesmo? Em muitas situações nas empresas, é uma abordagem univariada de tentativa e erro mesmo, ou seja, varia uma variável por vez e então verificamos o que acontece no processo.
Porém um processo real não se comporta desta forma, tudo varia ao mesmo tempo, então é preciso um método quantitativo adequado que seja capaz de compreender de forma correta o comportamento destes sistemas. Não temos mais tempo e dinheiro para atuação sem Administração Científica.
Uma coisa que acontece muito nesta área é a necessidade de quebra de paradigmas que, por questões culturais e até falta de visão do nível estratégico das empresas, ficaria difícil de colocar um “simples” 5 S para rodar em toda sua plenitude, inclusive disciplina para manutenção.
Muitas vezes passamos anos diante de um processo achando que o conhecemos bem. Se olharmos uma estatística macro no livro “A produtividade no chão de fábrica” de Tubino o nível sigma médio de indústrias brasileiras superam o patamar de 20.000 ppm de índice de rejeição. Mas vamos com calma: primeiro ppm quer dizer partes por milhão e índice de rejeição é um indicador que representa a quantidade de itens não conformes ou seja, itens que não atendem as especificações técnicas.
Portanto a cada 1 milhão de oportunidades, 20.000 são defeitos. A média mundial é em torno de 200 ppm e a referência é o Japão com 10 ppm.
E o que o Six Sigma tem a ver com esse indicador?
Bem, ser Six Sigma significa termos um nível de qualidade alto a ponto de o índice rejeição ser de apenas 3,4 ppm. As empresas que pertencem a esse público seleto são as chamadas World Class Enterprise.
Portanto, dá para perceber que estamos muito longe disso e ouvir que “sempre trabalhamos assim” e que “conhecemos bem o processo” não cola mais? Se não precisássemos otimizar processos estaríamos numa posição de destaque em termos de índice de rejeição. Por outro lado, não é motivo para desanimar e sim virar essa página entendendo que não temos mais problemas e sim oportunidades.
Precisamos entender que qualidade não é custo. Custo é retrabalho, reprocessamento. Novos indicadores de performance voltados à sustentabilidade, felizmente, cada vez mais conquistarão lugar de destaque no nosso dia a dia, como economia de baixo carbono e eficiência energética.
Portanto, reprocessamento é gastar recursos naturais novamente para produzir algo que já deveria estar pronto. Isso sem falar no refugo. Taguchi, importante estatístico e engenheiro, criador do Método de Taguchi de otimização de processos (base do Design for Six Sigma), já nos alertou sobre a necessidade de redução de variabilidade inclusive para minimizar perdas pagas pela sociedade.
Então de fato precisamos saber:
- Quais fatores influenciam significativamente Y?
- Como ajustar X de modo que Y tenha um valor satisfatório?
- Como ajustar X para minimizar a variação de Y?
- Como trabalhar bem mesmo na presença de ruídos externos (Z), o que em Six Sigma nós chamamos de processo Robusto.
O professor comenta que precisamos de fato aprender os conceitos e uso correto das ferramentas, senão corremos o risco de nos limitarmos a dizer que somos Green Belts e apenas reproduzir passos nos softwares estatísticos sem o real domínio sobre as técnicas que as empresas irão nos exigir.
Elas querem uma demonstração clara de impacto financeiro, aumento e manutenção de market-share. Para tal necessitamos de uma carga horária que permita o entendimento pleno da potencialidade dos métodos.
O conhecimento do especialista sobre o problema conjugado com a técnica (em casos especiais somando-se ainda o auxílio de especialistas em planejamentos de experimentos) irá permitir bons planejamentos, ou seja, mais rápidos, de menor custo e que possibilitem aos seus idealizadores responderem, baseado em inferência estatística, a resposta de seus problemas.
Imaginem um processo químico industrial que tem por objetivo maximizar o rendimento na conversão de matéria-prima em produto acabado.
Imaginem ainda que especialistas do processo levantaram possíveis fatores que possam influenciar essa resposta: vazão de alimentação do reator (L/min), teor de catalisador (%), taxa de agitação (RPM), temperatura (ºC) e concentração de reagentes (%).
Como gestores, os Belts são capazes de otimizar e discutir em detalhes um processo como este. Mas poderia ser outra aplicação e poderia ser um serviço. Escolhi aqui algo para ilustrar.
Ao conduzir alguns experimentos pautados na estatística do DOE, Green Belt estará apto a compreender que nem todas as variáveis de entrada impactam de maneira significativa o rendimento. É como se o DOE num primeiro momento atuasse como um filtro separando o joio do trigo apontando um Pareto para destacar as variáveis críticas.
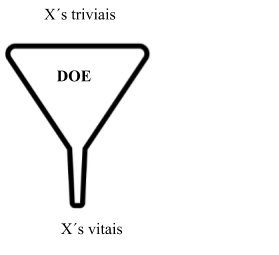
Neste exemplo, essas variáveis críticas seriam catalisadoras, temperatura e concentração. Estas variáveis então após ajustadas são sérias candidatas a serem numa próxima etapa (Control do DMAIC) monitoradas em rotina via Controle Estatístico de Processos (CEP).
Além disso, queremos saber de que maneira então teríamos que ajustar o processo a fim de maximizar o rendimento. Assim, o DOE nos revela que o melhor ajuste do processo são os níveis indicados em vermelho conforme Figura 3.

Devemos trabalhar com 10L/min de vazão, com 2 % de catalisador, 100 RPM de agitação, 180ºC de temperatura e 3% de concentração de reagente.
Gostaria nesse momento de destacar as duas variáveis mais importantes deste processo: o teor de catalisador e nível de temperatura. O Green Belt consegue conduzir uma análise gerencial como essa através de softwares estatísticos como o Minitab.
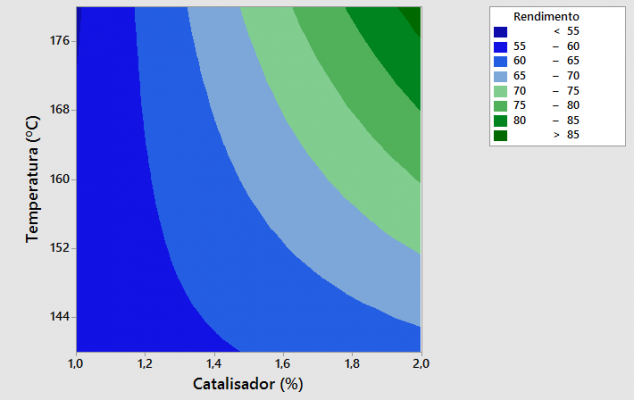
Já havíamos comentado sobre o ajuste dessas variáveis na Figura 3, porém a Figura 4 detalha o máximo de rendimento, conquistado numa faixa bem estreita destacada em verde escuro pela legenda. Então perceba que de fato ambas devem ser ajustadas nos níveis elevados para que o rendimento seja máximo. A falta de controle dessas variáveis de entrada causa variabilidade na resposta e o controle inadequado não leva a níveis ótimos de respostas. A mesma análise pode ser feita na Figura 5, porém em três dimensões:

O DOE também considera a possibilidade de efeito combinado entre as variáveis de entrada
Mas e se tivéssemos mais de uma variável resposta? Bem, é comum encontrarmos nas empresas processos assim, são os chamados processos com múltiplas respostas.
Neste caso utilizaríamos uma ferramenta poderosa do DOE que é capaz de atender simultaneamente a mais de um objetivo de otimização: a Desirability (“desejabilidade”).
Em termos mais práticos, podemos simultaneamente querer o máximo de rendimento e o mínimo de custo de produção ou até mesmo um produto com um valor nominal de densidade ou viscosidade por exemplo.
Assim, os Belts encontrarão uma solução única que atendam a todos ao mesmo tempo da melhor maneira possível.
Se quisermos reduzir ainda mais a quantidade de experimentos, darmos uma ênfase nos ruídos externos do processo e gerenciar um indicador que claramente aponta para redução de variabilidade de processos, aí destacamos uma nova dimensão do DOE que é o Método de Taguchi. Sem poesia, sem romance, com Engenharia de Taguchi.
Ficou interessado em aprender com propriedade como otimizar processos, reduzindo variabilidade, atendendo melhor às expectativas dos clientes e tudo isso com técnicas de metodologias ativas de ensino com abordagens teórica, didática e prática?
Venha fazer o curso de Green Belt Lean Six Sigma no IPOG!
O curso de Green Belt Lean Six Sigma de curta duração do IPOG é uma metodologia gerencial que reúne uma série de ferramentas estatísticas e de qualidade destinadas à análise e orientação da gestão dos processos de uma empresa, contribuindo com a busca e a adoção das melhores práticas e com o alcance de resultados cada vez mais qualificados e competitivos.
Neste curso, o aluno desenvolverá a habilidade de liderar projetos de melhoria utilizando a metodologia Lean Six Sigma e suas ferramentas, conseguindo:
- destreza na análise de dados resolver problemas complexos das organizações;
- ferramentas e técnicas para visualizar e organizar processos;
- liderar equipes em projetos de melhoria e
- gerenciar processos por meio de indicadores.
Com isso, os profissionais capacitados tornam-se notáveis, mais preparados para alcançar resultados significativos para suas empresas.
Entre em contato conosco agora mesmo e mude o seu futuro.